The Role of Linear Actuators and Air Motors in Factory Automation
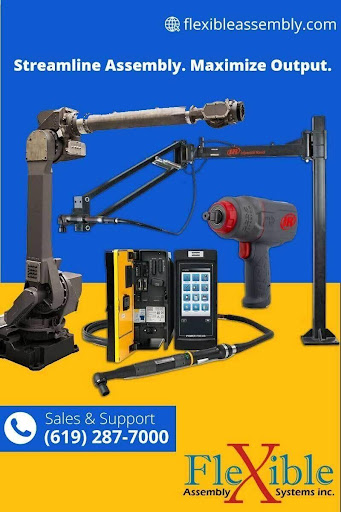
Factory automation relies on precise, reliable equipment to improve productivity and reduce costs. Linear actuators and air motors are two key components that allow automated systems to function efficiently. In this blog post, we’ll explore the purpose and benefits of using these devices in factory automation.
What are Linear Actuators?
A linear actuator converts energy into linear motion. It uses an electric motor or hydraulic cylinder to extend and retract a piston rod in a straight line. This linear push/pull movement allows linear actuators to automate tasks like:
- Opening and closing valves
- Locking doors or nudging them open
- Lifting equipment like robotic arms
- Pushing pallets or products along conveyors
- Transferring heavy loads in a factory
Compared to more complex pneumatic or hydraulic cylinders, electric linear actuators are simple to install and control. Their quiet operation also makes them suitable for use in labs, hospitals, and other sensitive environments.
There are several key reasons linear actuators are popular components in automated factories:
- Precise Movement – High precision linear actuators can position loads within 0.1mm accuracy. This allows them to perform quality assurance tasks and fine adjustments in manufacturing machines.
- Adjustable Speed and Force – Electric actuators allow users to program the rate and force produced on extension and retraction. So tasks can be performed quickly and safely.
- Low Maintenance – Electric models have few moving parts. Maintenance comes down to occasionally lubricating the screw or rail that guides the piston rod.
- Integration – Popular communication protocols like IO-Link allow actuators to connect to factory controllers and sensors. Making automation simpler.
How are Air Motors Used in Factories?
Air motors run exclusively on compressed air to produce mechanical motion energy. The simplest models convert pressurized air into rotary force to spin a shaft. But linear air motors also exist to provide linear push-pull movement.
Here are some common ways rotating vane and piston air motors are used:
- Turning Valves and Regulators – Compact vane air motors can replace manual handwheels to automate the opening and closing of valves.
- Powering Conveyors – Larger piston air motors drive the rollers on conveyor belts to smoothly transport products down the line.
- Lifting Platforms – Multi-vane air motors lift scissor arms to raise or lower work platforms and work tables.
- Torque Augmentation – Adding air motors to bolt runners boosts the delivered torque to tighten large bolts in heavy machinery.
Benefits of Air Motors
Air motors are simple, reliable, and economical. Here’s why factories take advantage of them:
- No Electricity Required – Air motors eliminate the costs and hazards of running electrical lines. And there’s no spark risk when used in explosive environments.
- Higher Starting Torque – Air motors can produce over twice the starting torque of comparably sized electric motors. Making them favored for cyclic start-stop applications.
- Intrinsic Safety – With no heat or spark generation, air motors themselves don’t pose ignition risks in hazardous industries like oil and gas, mining, and chemicals.
- Easy Speed Control – Throttling airflow through venturis gives users adjustable speed control over air motors without electronics.
- Lower Maintenance – Due to no brushes or commutator, rotary vane air motors in particular can operate for 10,000 hours before servicing.
Choose Flexible Assembly System for Factory Automation
Flexible Assembly System specializes in automated assembly solutions using precision linear actuators, air motors, and other automation components tailored to each client’s application. Our team brings decades of experience creating cost-effective systems with some key benefits:
- Maximized Uptime – We build automation with longevity and serviceability as priorities, using reliable name brand components.
- Adaptable Processes – Our flexible assembly cells allow model changeovers in minutes, minimizing downtime costs.
- Safe Collaboration – Our technology emphasizes human-robot collaboration, with multi-sensing safeguards.
- Improved Efficiency – From product concept to after-sales support, we offer turnkey solutions to help streamline operations.
Contact our application experts today to discuss your production challenges. Our team will conduct a thorough needs assessment before recommending an automation solution using linear actuators, air motors, or other technologies to save you time and costs.
How to Improve Efficiency Using Torque Arms and Screw Feeders
Two ways assembly plants can dramatically improve line efficiency are by incorporating torque arms and screw feeding equipment. Here’s a closer look at how these overlooked components can speed production and lower costs:
How Torque Arms Boost Productivity
Torque arms, also called torqueliners or toqueliners, are compact cylinder systems designed specifically for nut driving applications. They excel at repeatedly running down fasteners during high-volume assembly operations.
Torqueliners typically combine an air-driven vane motor with an integrated socket spindle. The operator loads the arm with nuts from a feeder bowl or tube. Then upon actuating the pistol grip handle, the socket quickly zips down the desired fastener.
Here are four ways this semi-automatic approach improves productivity over using traditional nutrunners:
- Faster Cycles – Eliminating the need manually load each fastener cuts the average tightening cycle time significantly. Some torque arms run as fast as 36 cycles a minute.
- Reduced Fatigue – By easing the repetitive force needed, toqueliners lessen hand and wrist fatigue. Allowing operators to comfortably sustain faster production speeds.
- Greater Consistency – Torque arms apply standardized torque values to every fastening sequence for improved joint quality assurance.
- Changeable Heads – Users can swap between different screwhead sockets in seconds to accommodate line changeovers. Minimizing downtime losses.
In short, torque arms let one operator drive many more fasteners per shift. Scaling production rates to keep pace with other bottleneck machinery.
Boosting Output With Screw Feeding Systems
Just like nuts and bolts, threaded screws are a fundamental fastener used in all types of products. Screws often arrive for assembly in simple bulk containers that require operators to manually pick and place each one from the bin.
But when dealing with small delicate electronics or handling thousands of fasteners per day,workers struggle to keep up. In these cases, automated screw feeding systems provide huge efficiency gains.
Vibratory screw feeder bowls rapidly orient and sort screws correctly into single-file lanes or flexible hose coils. This prepared supply then connects directly to screwdriving stations for hands-free operation. Operators simply have to maneuver parts under drivers lined continuously with screws.
Screw feeders offer these measurable improvements:
- Output doubled or tripled. One feeder reliably supplies multiple screwdrivers.
- Labor requirements cut 40-70%. Feeding screws is no longer an issue.
- Higher line UPH from near-continuous operation.
- Product damage reduced since no human handling.
- Improved quality control from screw feed consistency.
Adapting screw feeding discourages production bottlenecks upstream or downstream. And the systems prove easily scalable when throughput needs change.
Any facility driving high volumes of threaded fasteners should evaluate integrating screw feeders into their assembly process. Most discover it’s one of the quickest paths to boosting productivity and profits.
Source: The Role of Linear Actuators and Air Motors in Factory Automation